“ย่อง” มีความหมายว่า
ค่อย ๆ เดินเข้าไป แผ่วเบา และระมัดระวังตัวเพื่อให้ไม่ผิดสังเกตของใคร
และการเข้าไปเยี่ยมชมโรงงานประกอบรถยนต์ ของ มิตซูบิชิ มอเตอร์ส (ประเทศไทย) ครั้งนี้ เราก็สามารถเรียกได้ว่าเป็นการย่อง…
เพราะ ทริปนี้ เริ่มต้นอย่างง่ายๆ จนแทบไม่น่าเชื่อ จากอีเมล์ ฝากข่าวธรรมดาๆ ของทางมิตซูบิชิ ที่ส่งตรงถึงผมประชาสัมพันธ์การจัดทริป
ให้ลูกค้าผู้มีอุปการะคุณของเขา ได้เข้าเยี่ยมชมโรงงานประกอบรถยนต์ขนาดใหญ่ บนพื้นที่ในนิคมอุตสาหกรรมแหลมฉบัง เมื่อ 17-18 กุมภาพันธ์ที่ผ่านมา
ผมก็ตอบอีเมล์กลับไป สั้นๆ ขำขำ ออกแนวทีเล่นทีจริงว่า “อยากไปด้วย อยากไปด้วย อยากไปด้วย อิอิ”
ส่งกลับไปโดยไม่นึกฝันมาก่อนว่า จู่ๆ ตอนบ่ายในวันรุ่งขึ้น ทางฝ่ายประชาสัมพันธ์ ของ มิตซูบิชิ ก็จัดเตรียมทุกอย่างเอาไว้ให้ผมเรียบร้อย
อย่างรวดเร็ว! ดังนั้น งานนี้ ผม จึงพา BnN หนึ่งในสมาชิกของ The Coup Team ไปร่วมเยี่ยมชมโรงงานในครั้งนี้ด้วยกัน แถมยังเตรียมรถเอาไว้ให้เดินทางเสร็จสรรพ!
เพระาโดยปกติแล้วแทบทุกครั้งที่มิตซูบิชิ จัดทริปเยี่ยมชมโรงงาน จะต้องมีเหตุให้ผมไม่อาจมาร่วมงานได้เสมอๆ ดังนั้น ช่วงเวลาที่กำลังนั่งทำเว็บนี่ละั
คือช่วงเวลาที่เหมาะัสมมากสุดแล้ว อีกทั้ง ผมอยากจะดูให้เห็นกับตา ถึงลักษณะการทำงานของ พนักงานของมิตซูบิชิ ในแหลมฉบัง
อีกทั้ง ผมอยากจะมาดูบรรยากาศ ของการนำลูกค้า เข้าเยี่ยมชมโรงงาน ด้วยว่า ความรู้สึกของลูกค้า ที่มีต่อมิตซูบิชิ นั้น จะเป็นเช่นไร
เพราะตามปกติแล้ว การเข้าชมโรงงาน ของผู้ผลิตรถยนต์ค่้่ายอื่นๆ นั้น คุณจะต้องทำเรื่องผ่านฝ่ายประชาสัมพันธ์ ขอเข้าเยี่ยมชมเป็นหมู่คณะ
และต้องจัดคิว เตรียมนั่น ประสานนี่ กันวุ่นวายไปพอสมควร
แต่ มิตซูบิชิ กลับ จัดเชิญลูกค้า ให้เข้าชมโรงงานของตนเอง ซะเลย แถมได้ทราบมาว่า ในอดีตนั้น ทำกันมานานแล่้ว แต่ไม่ค่อยออกเป็นข่าว
ซึ่งนี่ถือเป็นเรื่องที่ดีมากๆ และน่าชมเชยมากๆ ที่ผู้ผลิตรถยนต์ จะเปิดบ้าน หรอื Open House ให้ลูกค้าของตน เข้าเยี่ยมชมกันเอง อย่างง่ายดาย
และไม่ต้องมีพิธีรีตรองอื่นใด มากมายไปกว่า ควรสวมหมวกหรืออุปกรณ์ด้านความปลอดภัยอื่นๆไำปด้วย
ดังนั้น ช่วงเช้าราวๆ 8 โมงเศษๆ ของ วันที่ 18 กุมภาพันธ์ที่ผ่านมา ใครที่ใช้บริการทางยกระดับ บูรพาวิถี มุ่งหน้าไปทางชลบุรี
คงจะพบเห็น Mitsubishi Pajero Sport 3.2GT สี Eissen Gray แล่นแซงผ่านหน้าคุณๆไปทางเลนขวา ถ้าใครตามมาทัน ก็จะสังเกตว่า
ทั้งคนขับ และผู้โดยสารนั่งข้างๆ กำลังเอร็ดอร่อยอยู่กับ อาหารเช้าของแมคโดนัลด์ รวมทั้งฮัชบราวน์ และเฟรนซ์ฟราย ไปพร้อมๆกับที่
ชุดเครื่องเสียง ALPINE ซึ่งติดตั้งมากับรถ และใช้งาน”โคตรยากลำบากเลย” กำลังเล่นแผ่น DVD ของวง Flure ไปถึง มิวสิควีดีโอ เพลงที่เราชื่นชอบกันอยู่

ความเป็นมาของโรงงานนี้ เป็นอย่างไร ก็คงต้องปล่อยให้ BnN เป็นผู้เล่าให้อ่านกันครับ
BnN : โรงงานประกอบรถยนต์ของ บริษัทมิตซูบิชิ มอเตอร์ส (ประเทศไทย) จำกัด ตั้งอยู่ที่นิคมอุตสาหกรรม แหลมฉบัง อำเภอศรีราชา จังหวัดชลบุรี ถูกก่อสร้างขึ้นด้วย
ทุนจดทะเบียนกว่า 7,000 ล้านบาท มีกำลังการผลิตรถยนต์ เพื่อส่งขายในประเทศปีละประมาณ 200,000 คัน ที่สำคัญไปกว่านั้น โรงงานแห่งนี้ ยังถูกมอบหมายจาก
มิตซูบิชิ มอเตอร์ส คอร์ปอเรชัน ประเทศญี่ปุ่น ให้เป็น ฐานการผลิตเพื่อส่งออก ของรถกระบะขนาด 1 ตัน L-200 ทั้งรุ่นเดิม สตราด้า และรุ่นใหม่ ไทรทัน ไปยังตลาดต่างๆ
กว่า 140 ประเทศทั่วโลก ด้วยกำลังการผลิตสูงถึง 800,000 คัน
ในพื้นที่ทั้งหมดนี้ มี 2 โรงงานย่อย นั่นคือ โรงงาน 1 สำหรับการประกอบรถยนต์นั่ส่วนบุคคล ทั้ง มิตซูบิชิ แลนเซอร์ สเปซแวกอน และ ปาเจโร สปอร์ต (แต่เราไมไ่ด้เข้าไปชมกัน
เนื่องจาก อยู่ในระหว่าง เตรียมการขึ้นสายการผลิต แลนเซอร์ รุ่นใหม่ โครงการ GS41 หรือรุี่นหน้าฉลามที่หลายๆคนรอคอยนั่นเอง
ส่วนโรงงานที่ 2 นั้น เน้นการประกอบรถกระบะ ทั้ง ไทรทัน และสตราด้า…นอกจากนี้ ยังมีพื้นที่สำหรับ โรงงาน ผลิตเครื่องยนต์ MEC ในละแวกใกล้เคียง
ผลิตเครื่องยนต์รวมแล้ว 10 แบบ ซึ่งนอกจากจะผลิตเพื่อป้อนตลาดเมืองไทยด้วยแล้ว ทุกวันนี้ มิตซูบิชิ มอเตอร์ส ประเทศญี่ปุ่น ยังต้องสั่งซื้อเครื่องยนต์
จากโรงงานในบ้านเรา เพื่อนำไปวางใน มิตซูบิชิ ปาเจโร V6 3.8 ลิตร รวมทั้งรุ่น ดีเซล เทอร์โบ 3.2 ลิตร ด้วย นั่นเอง!! อีกทั้งยังมีสนามทดสอบ
โกดังพักอะไหล่ รอประกอบ และพื้นที่แพ็คชิ้นส่วน CKD (Complete Knock Down) ไปยังโรงงาน ในตูนีเซีย และบราซิล เพื่อให้ทั้ง 2 โรงงานนั้น
ประกอบรถกระบะไทรทัน ขายในประเทศของตนเอง โดยจะไม่ได้ส่งออกต่อไปแต่อย่างใด
อ่านถึงตรงนี้แล้ว คุณผู้อ่านคงจะสงสัยว่า ทุกวันนี้ โรงงานแหลมฉบัง ยังประกอบรถกระบะรุ่นสตราด้า ขายอยู่อีกเหรอ? ทั้งที่ในบ้านเราเลิกทำตลาดไปนานแล้ว
ตั้งแต่ปี 2005 เหตุผลก็คือ ในบางประเทศ ยังมีการทำตลาดรถกระบะรุ่นดั้งเดิมนั้นอยู่ มิตซูบิชิ จึงยังต้องประกอบรถรุ่นนี้ เพื่อส่งออกไำปยังประเทศเหล่านั้นต่อไป
ปัจจุบัน กำลังการผลิตของโรงงานแหลมฉบัง ถูกปรับลดลง เมื่อเดือนธันวาคมที่ผ่านมา เนื่องจากปัญหาวิกฤติด้านเศรษฐกิจ ที่ลุกลามไปทั่วโลก
อย่างที่ทุกท่านทราบกันดีอยุ่ จากเดิม มี 2 กะเวลา แต่ปัจจุบัน ลดเ้หลือ แค่ กะกลางวัน 8.00-17.20 น. (9 ชั่วโมง 20 นาที) เพียงอย่างเดียว
นอกจากนี้ ยังลดปริมาณการผลิตลง จากระดับ 30 คัน/ชั่วโมง เ้หลือเพียง 25 คัน/ชั่วโมง หรือตีเสียว่า จาก วันละ 720 คัน เหลือเพียงวันละ 225 – 250 คัน
โดยประมาณ
ที่นี่ ใช้ระบบการผลิตแบบ Just-in-time หรือ คัมบัง อันเป็นแนวคิดมาจาก โรงงานของ โตโยต้า มอเตอร์ นั่นเอง โดยระบบนี้ จะไม่มีการสต็อกอะไหล่
แต่จะใช้ระบบสั่งซื้อคอมพิวเตอร์ ผ่านระบบออนไลน์ ตรงสู่ผู้ผลิตชิ้นส่วน ซึ่งจะต้องจัดเตรียมชิ้นส่วนให้ทันกับเวลาที่ รถบรรทุกจากทางมิตซูบิชิว่าจ้าง ไปรับมาเอง
แวะรับตามซัพพลายเออร์ต่างๆ ตามใบงานที่กำหนด ก่อนจะขับกลับมาที่โรงงาน ระบบนี้ เรียกว่า ระบบ MilkRun เพิ่งถูกนำมาใช้ เมื่อ 5 ปีที่ผ่านมา
และผลของมันก็คือ ช่วยลดความวุ่นวาย ในการจัดการกับชิ้นส่วนอะไหล่จากซัพพลายเออร์ อีกทั้งยังช่วยลดความแออัดคับคั่งของการจราจร ในโรงงาน
เป็นผลพลอยได้อีกต่างหากครับ
J!MMY : 10 โมงกว่า ได้เวลา เข้าเยี่ยมชมโรงงานกันแล้วเราถูกแบ่งออกเป็น 3 กลุ่ม และแน่นอน ผมกับ BnN ขออยู่กับกลุ่มสุดท้าย คนน้อยๆ เดินสบายๆ ไม่รีบร้อน
จุดที่ทางมิตซูบิชิ ไม่ได้ให้เราเข้าไปชม เนื่องจากเหตุผลด้านความปลอดภัยนั้น มี อยู่ 2 จุด
จุดแรกนั่นคือ ขั้นตอนการเชื่อมแผ่นเหล็กรูปแบบต่างๆ ที่กำหนดไว้ ให้เป็นโครงสร้างตัวถัง White Body เพราะอาจเกิดอันตรายจากประกายไฟ ที่พุ่งไปพุ่งมา
ในระยะไกล อย่างสนุกสนานของมัน แต่ไม่สนุกกับร่างเรา ในขั้นตอนการเชื่อมโลหะนั้น ใช้หุ่นยนต์มาช่วยงาน ในหน้าที่ซึ่งต้องการความละเอียด หรืออาจเป็น
อันตรายต่อมนุษย์ได้ มากถึง 8 ตัว มิตซูบิชิ แตกต่างจากโรงงานประกอบหลายๆแห่งที่ผมเคยไปชมมา นั่นคือ ในพื้นที่เชื่อมโลหะนั้น จะมีม่านที่เห็ยรายล้อมรอบ
เพื่อป้องกันไม่ให้ลูกไฟ กระเด็นออกไปนอกพื้นที่ ที่กำหนด

และในขั้นตอนนี้จะมีการตอกเลขตัวถัง ตรวจสอบคุณภาพ จากนั้นเจ้าหน้าที่ในไลน์ผลิต จะคีย์ข้อมูล ลงในระบบคอมพิวเตอร์ เพื่อช่วยควบคุมกำลังการผลิต
ออกเอกสารสำหรับแจ้งให้กับพนักงาน ในไลน์ประกอบ ได้ใส่ชิ้นส่วนอะไหล่ให้ถูกต้อง ตามออร์เดอร์ ของทั้งใน และต่างประเทศ

จุดที่ 2 ก็คือ เมื่อเตรียมพื้นผิวตัวถังเรียบร้อยแล้ว โครงสร้างตัวถัง White Body ก็จะถูกส่งเข้าไปยังห้องพ่นสี โดยจะถูกชุบลงไปในบ่อสีป้องกันสนิม EDP
เหมือนเช่นที่โรงงานประกอบรถยนต์ทั่วๆไปเขาทำกัน โดยหัวรถจะทิ่มลงไปในบ่อเสียก่อน จากนั้น เมื่อตัวรถ จมลงจนมิดระดับสีในบ่อแล้ว
เพื่อให้มีอากาศถ่ายเท และลดฟองอากาศ ซึ่งอาจมีผลต่อคุณภาพของชิ้นงานที่ออกมาได้ในภายหลัง
สายพานจะลากโครงสร้างตัวถัง ไปอย่างช้าๆ เพื่อให้สี EDP ซึมเข้าไปทุกอณูของเนื้อเหล็ก ในทุกจุด โดยจะมีท่ออากาศ ยื่นออกมาเหนือผิวน้ำในบ่อ
เมื่อโครงสร้างตัวถัง ถูกยกขึ้นเหนือผิวน้ำ ก็จะเข้าสู่กระบวนการอบแห้ง และตรวจสอบ อีกรอบ ก่อนจะเข้าสู่ห้องพ่นสี
โรงงานแหลมฉบังแห่งนี้ ใช้ หุ่นยนต์พ่นสี มากถึง 6 ตัว
ขณะเดียวกันน้ำที่เหลือจากกระบวนการต่างๆ จะถูกนำมาผ่านระบบบำบัดน้ำเสีย เพื่อให้น้ำทิ้ง สะอาดที่สุดเท่าที่จะเป็นไปได้

และการเริ่มต้นทัวร์ของเรา ก็เริ่มจากตรงนี้…

จุดที่ชุดเพลาขับด้านท้าย จะเริ่มวางลงบนเฟรมแชสซีก่อน ตามด้วย ระบบกันสะเทือน ระบบเบรก ทั้งหน้า-หลัง และปีกนกต่างๆ ขณะเดียวกัน เครื่องยนต์
อันเป็นผลผลิตจากโรงงาน MEC ก็จะถูกส่งมาจากสายพานด้านบน คนงานจะกดรีโมท ปล่อยเครื่องยนต์ และชุดเกียร์ ให้ลงมาประกบวางลงบนโครงสร้างเฟรมแชสซีช้าๆ

ขณะเดียวกัน หลังจากผ่านกระบวนการอบแห้ง และ ตรวจสอบคุณภาพเรียบร้อยแล้ว โครงสร้างตัวถังจะเริ่มถูกลำเลียงเข้าสู่สายการผลิต คนงานจะเริ่มติดตั้งชิ้นส่วนประกอบต่างๆ
จนพอจะมีเค้าโครงการเป็นตัวรถบ้างแล้ว จึงจะค่อยๆ ปล่อยลงมาจากสายพานด้านบน มาวางประกบกับเฟรมแชสซี โดยหัวเก๋งจะถูกวางลงมาก่อน ตามด้วยส่วนกระบะท้าย
ขันน็อต และจุดยึดต่างๆให้แน่น
เมื่อถึงสถานีนี้ ประตูรถ ที่มีอยู่ กี่บานก็ตามแต่ จะถูกถอดออก ลำเลียงขึ้นสายพาน
BnN : การแยกประตู ก่อน ค่อยมาประกบกับตัวถังในภายหลัง นั่นเพราะ การติดตั้งชิ้นส่วนในตัวรถนั้น ต้องการความคล่องตัว หากพนักงานในไลน์ ต้องเดินหลบประตูไปมา
นอกจากจะเสียเวลาแล้ว บานประตูเอง อาจเกิดรอยขีดข่วนได้โดยไม่ตั้งใจ ดังนั้น โรงงานประกอบรถยนต์ส่วนใหญ่ จึงจับแยกประตู ไปประกอบชิ้นส่วนที่เกี่ยวข้อง
ทั้งแผงประตู กระจกหน้าต่าง และ Trim ต่างๆ ให้เรียบร้อย เสียก่อนจะมาประกบกับตัวถังรถอีกครั้ง

เมื่อถึงจุดนี้ ชิ้นส่วนต่างๆ ภายในตัวรถ จเริ่มทะยอยถูกติดตั้งเข้าไป ตามแต่ละออร์เดอร์ ที่ลูกค้าสั่งเอาไว้ พนักงานต้องตรวจเช็คให้ดีๆ ว่า สต็อกของอะไหล่
ที่รถวิ่งอะไหล่เอามาวางแหมะให้ในสถานีของตนนั้น มันตรงกับใบออร์เดอร์ ที่แปะมาแต่แรกกับตัวรถหรือเปล่า
การทากาว เพื่อยึดติดกระจกหน้า่ต่างบังลมหน้า และหลัง นั้น โรงงานของมิตซูบิชิ ยังคงใช้แท่นหมุน เพื่อยึดกระจกเอาไว้ แล้วให้พนักงานทากาวหลอด
โดยรอบ ซึ่ง เมื่อเทียบกันแล้ว โรงงาน ของ GM ที่ระยอง ก็ใช้วิธีการเดียวกัน แต่โรงงาน ของ Toyota ที่บ้านโพธิ์ ดูเหมือนจะทันสมัยกว่า คือ ใช้หุ่นยนต์
ทำหน้าที่นี้แทนทั้งหมด ซึ่งปริมาณของกาว จะสม่ำเสมอกว่า เพราะทาในตำแหน่งที่มีการโปรแกรมกันไว้แล้ว โดยรอบ
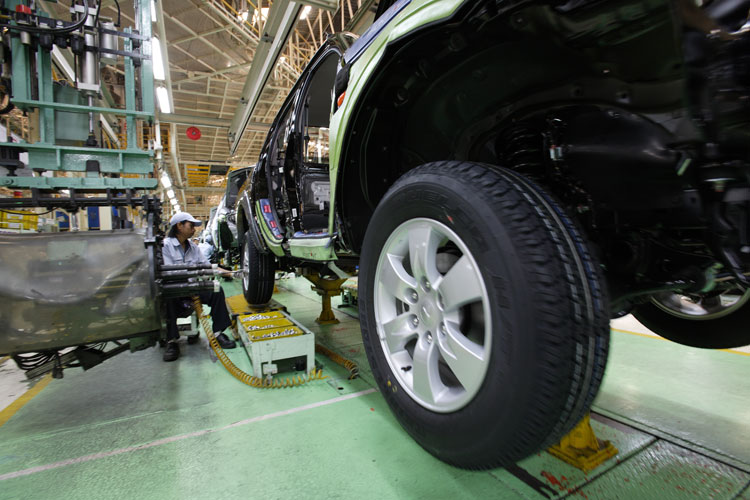
ในไลน์ เหมือนกับว่า เวลาที่ พนักงาน กำลังขันน็อตยึดต่างๆ เหมือนว่าจะยังขันไม่แน่นเลย
ความจริงแล้ว ประแจปอนด์ ที่เขาใช้นั้น จะมีการล็อกค่า Torque เอาไว้อย่างเหมาะสมแล้ว เพราะน็อตในบางตำแหน่ง
ถ้าขันยึดแน่นเกินไป ย่อมไม่ดีนัก มันอาจจะล็อกตาย หรือทำให้การขันถอดประกอบในครั้งต่อไป อาจไม่สมบูรณ์ได้
เมื่อใส่ล้อทั้ง 4 เรียบร้อย และขันแน่นตามค่าที่กำหนดแล้ว สายพานจะยกตัวรถ ขึ้นลอยข้ามผ่าน ทางเดินหลักของโรงงาน
เหตุที่ต้องยกข้ามไป เพราะ บริเวณนั้น เป็นทางเดิน กลางโรงงาน เพื่อลดเวลาในการเดิน และ การสัญจรของรถรางส่งอะไหล่ ภายในโรงงาน

การติดตั้งเบาะ ใช้หุ่นยนต์ ลำเลียงเบาะ เหมือนกับโรงงานประกอบรถยนต์แห่งอื่นๆ โดยชุดเบาะจะถูกลำเลียงมาตามสายพาน แบ่งแยกออกไปตามตำแหน่ง
เบาะซ้าย หรือขวา จะเป็นเบาะแบบม้านั่งยาว หรือเบาะแบบแยกก็ตาม คอมพิวเตอร์ จะจัดการแยกฝั่ง ให้เหมาะสม เพื่อลดเวลาการประกอบ และการเคลื่อนไหว
ของคนงานในไลน์ผลิต

ถึงสถานีนี้ ประตูจะกลับมาเจอกับญาติพี่น้องของมันอีกครั้งหนึ่ง คราวนี้เจอกันถาวร
แถมด้วยการเติมสารหล่อลื่น และน้ำยาหล่อเย็นต่างๆ หากเป็นน้ำมันเครื่อง จะเป็นของ DIAQUEEN ของมิตซูบิชิ โดยตรง
แต่สำหรับน้ำมันเกียร์อัตโนมัตินั้น ใช่น้ำมัน ATF-II

จากนั้น จะเข้าสู่ขั้นตอนการติดตั้ง อุปกรณ์พิเศษต่างๆ ตามแต่ละคัน
การบริหารจัดการในเรื่องนี้ ไม่ใช่เรื่องง่ายๆ เพราะทุกวันนี้ ไทรทัน มีทางเลือกออพชันมากถึง 120 รุ่นย่อย และมีอุปกรณ์ที่แตกต่างกัน ตามแต่ละตลาด
มากถึง 2,000 กว่า รูปแบบ!!
BnN : ดังนั้น ใบรายการที่แปะไว้ตั้งแต่โครงสร้างแชสซีแต่แรก จะช่วยให้พนักงานในไลน์ประกอบ ได้รู้ว่า จะต้องหยิบอุปกรณ์ไหน ติดตั้งเข้าไปบ้าง ในแต่ละสถานี
โดยมี รถลำเลียงชิ้นส่วน มาจัดส่งให้ถึงไลน์ผลิต ตามกำหนด ทั้งหมดนี้ควบคุมด้วยระบบคอมพิวเตอร์

เมื่อการประกอบเสร็จสิ้นลง รถจะไหลเข้ามายัง เครื่องทดสอบ และปรับตั้งค่าต่างๆ ทั้งค่ามุมองาของล้อ ค่าไฟหน้า ฯลฯ

จากนั้น เข้าสู่สถานีตรวจสอบระบบเบรก ทั้งด้านหน้เา และหลัง เพื่อให้มั่นใจว่าทุกระบบทำงานสมบูรณ์แบบของมัน

รวมทั้งการวัดปริมาณไอเสียจากเครื่องยนต์ ว่าผ่านเกณฑ์ที่เขากำหนดกันไว้หรือเปล่า
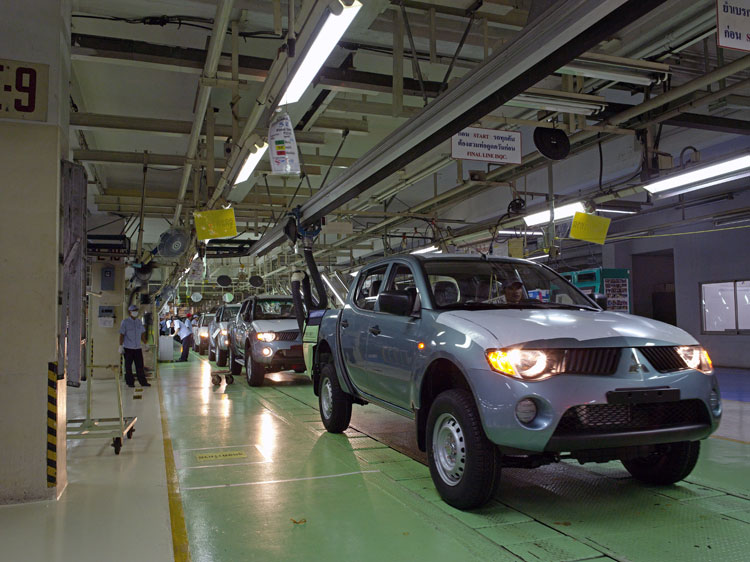
ถ้าผ่านรอดออกมาได้ ยังเหลืออีก 2 ขั้นตอน ที่สมาชิกใหม่บนถนนโลก จะต้องผ่านให้ได้

ด่านแรก ก็คือ Shower Test คือการปล่อยน้ำออกมา เพื่อหารอยรั่วซึม ตามจุดต่างๆ หากมี ก็จะแยกรถที่มีปัญหาในไลน์ประกอบ
ให้ได้ค่าที่ผู้ผลิตกำหนดมามากที่สุด มาทำการปรับแก้ ที่ข้างๆไลน์ผลิต กันเห็นๆ

ด่่านสุดท้ายคือ นำรถที่ผลิตได้ ออกไปแล่นทดลองขับ ว่ามีปัญหาอะไรหรือไม่ในช่วงระยะแรกๆ ที่ใช้งาน
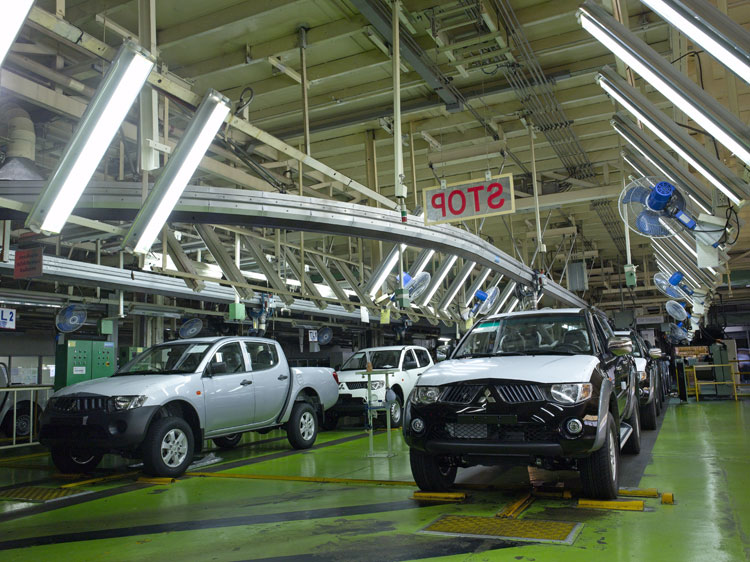
BnN : หลังจากการทดสอบหารอยรั่ว รถทุกๆคัน ก็จะถูกนำไปแล่นทดสอบในสนามด้านหลังของโรงงาน ครั้งสุดท้าย เพื่อให้มั่นใจว่า ทุกระบบทำงานสอดประสานกันอย่างดี และเมื่อผ่านการตรวจสอบคุณภาพอันเข้มงวดทุกๆด่านแล้ว รถยนต์ที่ประกอบเสร็จสิ้น ก็จะถูกนำไปจอดพักไว้ ณ พื้นที่จอดเก็บรถยนต์เพื่อรอการขนส่งไปยังผู้จำหน่ายในประเทศ หรือ ส่งขึ้นเรือ ซึ่งจอดรออยู่ ณ บริเวณ A5 ของท่าเรือแหลมฉบังต่อไป เพื่อส่งต่อไปยังอีกกว่า 140 ประเทศทั่วโลก
J!MMY : เท่าที่สัีงเกตการณ์ดู ผมพบว่า ลูกค้า แทบทุกคน แม้ว่าอาจยังมีคำถามคาใจ เกี่ยวกับตัวรถ และการบริการต่างๆ แต่แทบทุกคน ประทับใจกับการต้อนรับที่อบอุ่น
อารมณ์ Welcome Home เปิดบ้านพาเที่ยว รวมทั้ง อาหารมื้อเที่ยงที่จัดเลี้ยงให้กับลูกค้า มีของที่ระลึกติดไม้ติดมือกลับบ้าน นิดๆหน่อย ซึ่ง ทั้งหมดนี้
เป็น ระดับเดียวกับที่ สื่อมวลชน ทั่วไปได้รับและสัมผัสเช่นเดียวกัน ไม่มีเหลื่อมล้ำต่ำสูงกันเลยแต่อย่างใด
กิจกรรมดีๆ แบบนี้ ควรจะจัดอีก เรื่อยๆ อย่างน้อย 3 เดือน/ครั้ง ปีละ 4 ครั้ง มีกันให้ครบทุกไตรมาส
เพราะนี่ละ คืออีกช่องทางหนึ่งที่จะทำให้ ผู้ผลิตรถยนต์ ได้ใกล้ชิด และรับฟังปัญหาจากผู้บริโภคโดยตรง
อีกทั้ง สามารถนำไปประสานงาน แก้ไขปัญหา ติดตามผลให้กับลูกค้าต่อไปได้ แถมยังสานสัมพันธ์ลูกค้าเก่า
สร้างความรู้สึกที่ดี ให้ยิ่งผูกพันมากขึ้นไปอีก แถมงบประมาณที่ใช้ ก็ไม่ต้องมากมายนัก ประหยัดงบได้อย่างดีอีกต่างหาก
แล้วจะมีเหตุผลอื่นใดละ ที่ค่ายอื่น จะไม่ควรทำตาม?
คำตอบจากผมคือ “ไม่มี”
————————————///————————————–
J!MMY & BnN
20 กุมภาพันธ์ 2009